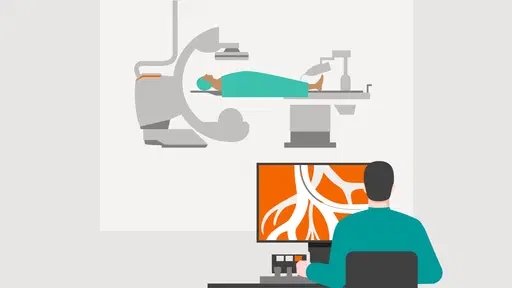
Verification Testing for Surgical Robot
TEAMMATES
Electro-Mechanical (EM) Team Manager
EM Senior Engineer (Design Verification Test lead)
ROLE
Took ownership of robot-to-catheter force testing under the supervision of senior engineers as part of the Electro-Mechanical (EM) team.
CHALLENGE:
Ensuring Robot Compliance with Catheter Force and Wire Torque Requirements
The neuroendovascular robotic platform needed to meet stringent force and torque requirements for safe and precise navigation through delicate vascular pathways. Verifying these parameters required custom testing setups and accurate data analysis.
SOLUTION:
Ensured robot precision and safety through rigorous testing and data-driven analysis.
Conducted over 40 tests to verify robot force and torque performance.
Built and optimized electromechanical test fixtures, troubleshooting transducer setups to ensure accurate readings.
Created 10 Design Controls documents to ensure compliance and traceability.
Developed MATLAB algorithms to automate data processing from Simulink, generating clear test reports and conducting statistical t-tests to flag potential failures.
Conducted 40+ Design Verification tests
Engineering Verification Testing
Performed pre-Design Verification system tests for 9 catheter/wire devices
Built, troubleshooted, and redesigned electromechanical test fixtures
Debugged force transducer setups
Created test methods, test reports, and fixture use documentation
Created 10 Design Control documents
Developed 3 Test Fixtures
Data Processing & Analysis
Programmed MATLAB algorithms to process Simulink data and automatically generate results summaries for Test Reports
Script sets up and performs statistical t-tests to flag potential system requirement failures
Assessed results to verify robot met force and torque requirements
Statistical Analysis with MATLAB & Simulink
Design for Assembly (DFA)
Collaborated with technicians to kit, build, and assemble subsystems for an Alpha system prototype
Designed 3 Build Fixtures & Assembly Tools